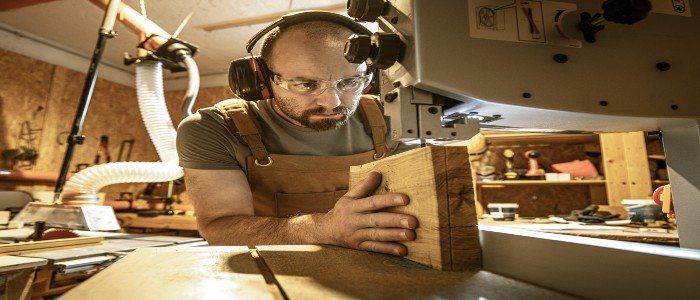
As a carpenter, your business faces a unique set of risks and hazards.This line of work may involve the operation of heavy or technical machinery, The use of tools, as well as manual labour in harsh conditions.The Canadian Centre for Occupational Health and Safety (CCOHS) classifies carpentry as performing one or more of the following: Measure, cut, shape, assemble, and join materials. Read, prepare, and interpret blueprints and drawings. Prepare cost estimates and documentation for clients. Use, clean, and maintain various equipment and tools. The Government of Canada projects that from 2017-2026 there will be 27,800 new job openings for carpenters.
1 As this industry continues to grow and evolve, so do the associated risks.Whether you are thinking of going into business, currently operate a business, or actively work as a carpenter, health and safety should be a primary concern. Are you ready to get your hands dirty and build a solid carpentry risk assessment program? Lay down a strong foundation with the guidelines below. Step 1: Assessing your risks A good carpentry risk assessment will consider unsafe situations where health and safety may be compromised.This includes but isn’t limited to: Exposure to loud noise from machinery and tools. Exposure to moulds, fungi and bacteria that could cause dermatitis, allergic reactions, or respiratory problems. Exposure to certain carcinogens that can cause cancer, including wood dust. Risk of pain or injury from working in awkward positions, performing repetitive tasks, or lifting. Risk of eye injury from flying particles. Exposure to extreme temperatures when working outdoors. Look around at your environment.
What type of materials are you working with? What do you use to do your work and where are you? Asking yourself these questions will assist in the management of your property and team of carpenters and ultimately help avoid fires, thefts, and injury. Here are a few examples of questions to assess your equipment and materials: Do I work with any flammable or combustible liquids? If so, how do I currently store them? Do I follow safe lifting techniques? Am I following current CCOHS standards when it comes to safe handling of tools and equipment? How do I currently dispose of waste and debris? Am I properly regulating the amount of materials onsite? Are they being properly stored and secured? Is there a clear emergency procedure? Do I have this posted in a visible place? Next, think about your team.Whether your carpenters have been in the field for years or have just finished an apprenticeship program, consider periodic refresher training to brush up on health and safety as it relates to the workplace.If you work with woodworking machines or hand and/or powered hand tools, ensure all workers know how to safely operate them and assess their skills. Other questions you can ask to help assess your team of carpenters include: Have I conducted thorough background checks on each worker? Is everyone familiar with the common hazards associated with the equipment and/or materials we work with? Does everyone wear the proper personal protective equipment? Is everyone taking the appropriate amount of breaks? Are my employees stressed or exhausted? Does everyone know how to report an incident or a hazard onsite? Step 2: Responding to your risks Once you have identified the key risks your business faces, evaluate your current mechanisms in place to mitigate them.
Consider the implementation of a loss prevention program where you are committed to adhering to certain standards that protect your property and employees.This will vary depending on the scope of your work, your team, and the size of your business. Loss prevention is the shared responsibility of both employees and management.Below, we’ve outlined what each group brings to the table when it comes to a proactive risk management approach: Management Provide a safe workplace, tools, equipment, etc. Provide a loss prevention program including creating, implementing, monitoring, and supporting the program through training, supervision, analysis, and documentation. Provide adequate management controls for loss prevention by identifying, communicating, and controlling hazards throughout the business. Review incident reports and ensure prompt corrective action. Monitor the loss prevention program for application and effectiveness, modifying if necessary. Evaluate how effectively employees follow standards of health, safety, and loss prevention and include this in performance reviews. Regularly review loss prevention activities with employees. Employees Actively participate in all aspects of the loss prevention program, including: training, evaluation of performance, and documentation. Understand the safe handling procedures of all tools and equipment. Clarify any uncertainty with management regarding any processes or rules in place. Maintain a safe working environment through regular inspection and cleaning. Be familiar with the reporting process in the event of an incident or potential risk. Step 3: Review, evaluate, and improve your risk response Once you have completed your carpentry risk assessment and successfully launched a loss prevention program, monitor how well it performs.
Continuously review your policies and schedule check-in points with employees to gather feedback.Hold periodic refresher training throughout the year, and whenever the program is significantly updated.Consider hiring a third-party, such as a risk management consultant or an insurance company, to evaluate the program’s effectiveness. Build a stronger future with the right experts At TruShield, we know there’s nothing small about your business.
We’re here to help you build a safer and brighter future by providing tailored carpentry insurance that meets your needs.Visit the skilled trades section of our website to learn more!
This blog is provided for information only and is not a substitute for professional advice.We make no representations or warranties regarding the accuracy or completeness of the information and will not be responsible for any loss arising out of reliance on the information.
Publisher: TruShield Insurance